
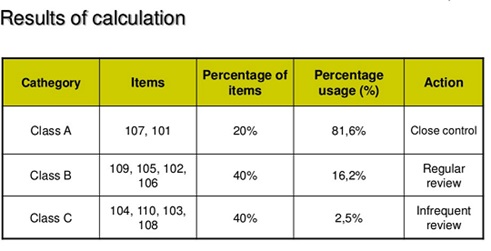
Unfortunately, maintenance operations cannot schedule for an equipment breakdown. This is relatively easy for manufacturing because one can better schedule for when the parts are needed. These are often the companies that end up going under.īut with a Just-In-Time system, the ordering of the part is scheduled so that it arrives shortly before it is needed. This expedited shipping can result in excessive costs that may go unnoticed as long as the company is still profitable. Many operations are operating in a reactive mode where parts are usually rush-ordered as needed.
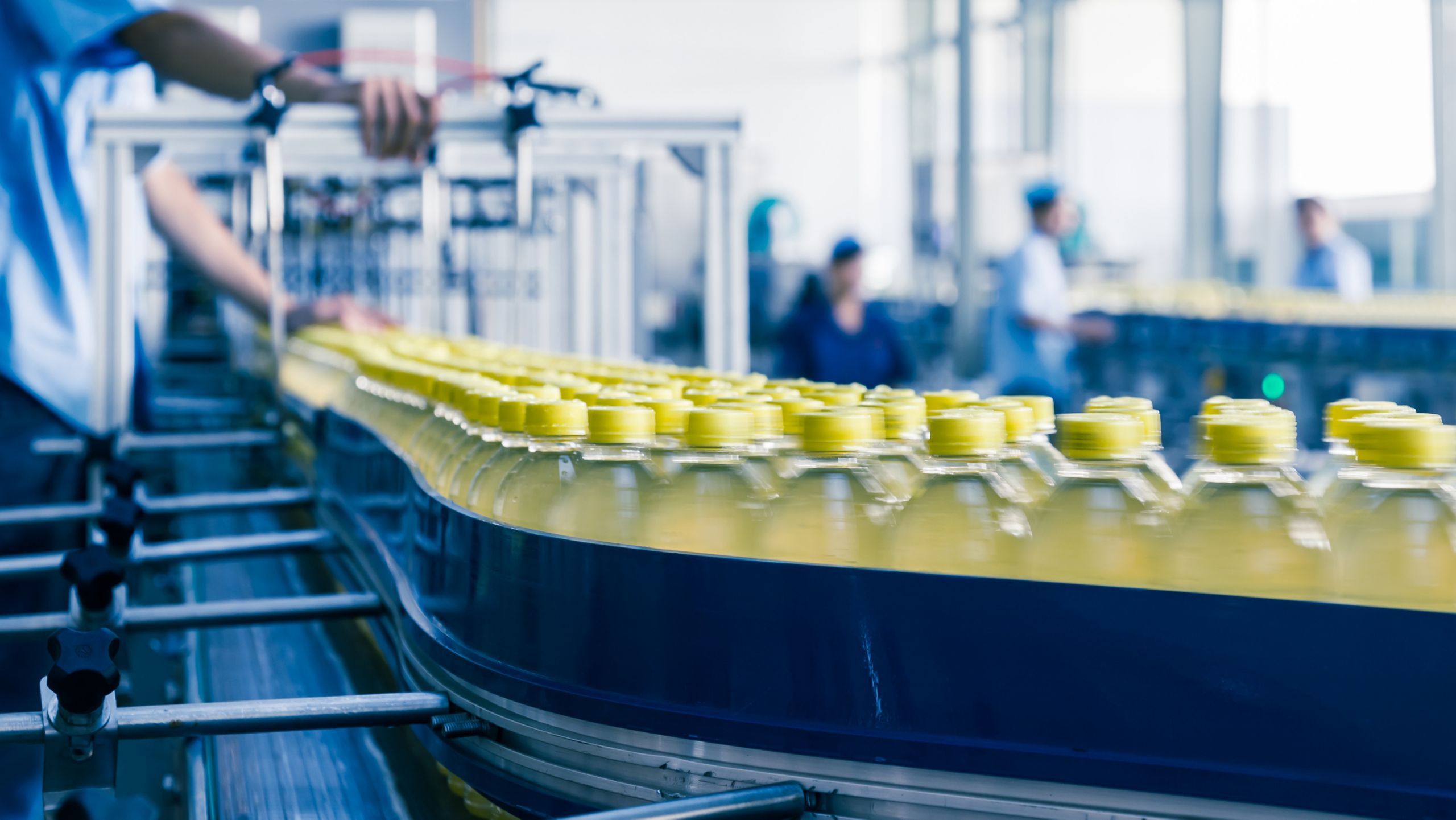
Unfortunately, this is not the case in many operations. If the storeroom and inventory are well organized and re-order points are used, plants generally will do very well. Based on lead time, parts usage history and consequences of not having the part when needed, one can determine re-order points and appropriate quantities to purchase. This initial cost yielded a savings of approximately $1,800 over the six weeks.īut the overstock/under-stock situation can be avoided. Although the higher-quality cutter was more than twice the price of the original, it lasted six times longer. The MRO buyer decided to seek alternatives and eventually found a higher-quality cutter for $1,200. These utters were poor quality and needed to be replaced every week. For instance, a construction company was using diamond cutters that cost $500 each. This allows the MRO buyer to comparison-shop the parts in order to find the ones that meet the specifications at the cheapest prices.Īlthough the low price of a part can be appealing, it may not always be the best choice in the long run. The key for the MRO buyer is to focus on the specifications (HP, RPM, frame size, etc.) of the required parts. In fact, one can often find the same part for a fraction of the cost under a generic name. Just like pharmaceuticals, the costs of generic parts are much lower than brand-name parts. There are a couple of ways that this can be accomplished. When locating parts, you want to ensure that you select a quality part at a reasonable price.
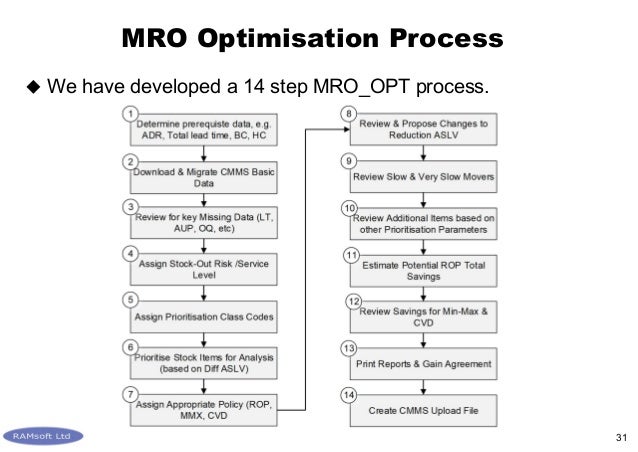
Properly managing MRO inventory has proven time after time to save 10 – 30% of annual inventory dollars. You’re losing a lot of money despite the part being there. Sometimes the part is in the storeroom, but you can’t find it so you have to go through the process of locating a vendor, finding the part and ordering it. If equipment is down and a required part is unavailable, that breakdown could cost you a tremendous amount of money because until the equipment is fixed, revenue is lost. Effective MRO parts management is crucial to maintenance productivity and reliability.
